FINANCIAL
%
IMPACT
LABOR
%
- Project Summary
- Situation
- Typical Invasive Repairs
- Revive Pipes Solution
- Revives Multi-Story CIPP Services
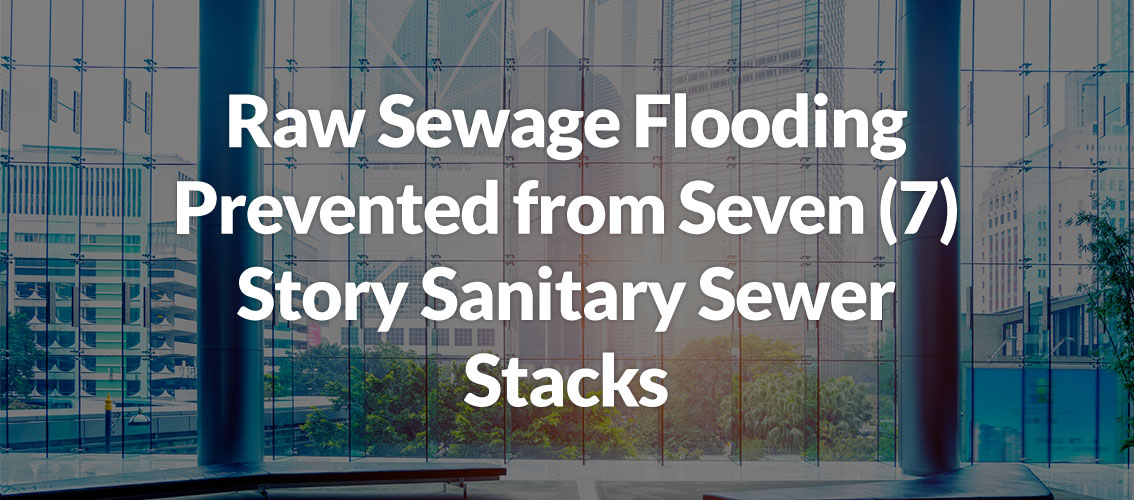
A seven (7) story residential complex experienced several incidents of nasty flooding and raw sewage contamination due the corrosion cracking of four (4) sanitary drain stacks over only a couple of years.
When Revive Pipes was contacted, we performed video inspections and provided an assessment on the remaining sanitary drain stacks in the building. Much of the cast iron drain pipe was experiencing pinhole leaks that were calcifying and sealing off on their own. These type of pinhole leaks are a warning sign that the piping system is at the end of its useful life.
Continuing to use the sanitary sewer stacks in the corroded, pitted and deteriorated condition that they were in would have resulted in more nasty flooding, damage to the facility and upset tenants. The property manager and building owner made a prudent decision to proactively install Cured in Place Pipe (CIPP) structural liners in the three (3) remaining original wastewater stacks in the most critical condition.
The property management company for the building had worked with Revive Pipes in the past and was aware of our capabilities so they contacted us to look at the roof drain problem. Revive Pipes installed Cured in Place Pipe (CIPP) structural liners in all twenty-one (21) of the roof drains in the newly replaced roof to seal the Mechanical Joints (MJ). The building owner wanted to install liners in all of the roof drains rather than only the four (4) roof drains that were found to be leaking to give them certainty moving forward that they would not have leaks from any of the roof drains in the future. Our non-invasive roof drain repair didn’t disturb the newly replaced roof membrane, which would have created more uncertainty about potential leaks in the future.
Revive Pipes installed Cured in Place Pipe (CIPP) structural liners in three (3) remaining sanitary sewer stacks saving the building and its tenants from impending floods of raw sewage and the subsequent disruptive cleanup and sewer stack repair. The building owner saved 30% on the cost of a traditional wastewater stack replacement, no tenants were displaced from their units and contractor time on site was reduced by 80%.
Prior to finding out about Revive Pipes innovative sewer replacement service, the property endured the typical sewer stack replacement on the first four (4) vertical stacks.
Each vertical stack took 1 ½ to 2 months to replace by the time all floors were completed.
- Tenants in the immediate vicinity of the work area had to be vacated while the work was being completed on their floor
- Work areas on each floor had to be sealed off to decrease the amount of dust entering tenant spaces
- Walls on each floor were torn out from floor to ceiling to access the pipe.
- Cinder block chases where the sewer stacks ran were busted open from floor to ceiling
- The corroded old cast iron pipe was cut out and the raw sewage contaminated pipe had to be wrapped and sealed before carrying it out of the building to be disposed of in a specialized landfill for biohazards
- The new cast iron pipe was installed
- Toilets and sinks were reconnected to the wastewater stack
- Cinderblocks were reinstalled in the chase
- Drywall was reinstalled and taped, mudded and sanded
- Walls were repainted
- Cleaners vacuumed and wiped up all residual construction dust that wasn’t contained within the work enclosure
Revive Pipes removed the corrosion buildup in the remaining sanitary stacks and installed Cured In Place Pipe (CIPP) structural liners in 3 of the most problematic remaining stacks in only 6 days. Our specialized tools, equipment and techniques allowed us to provide a non-invasive sanitary sewer stack repair to our client.
Revive Pipes is able to install Cured in Place Pipe (CIPP) structural liners in multi-story buildings regardless of how many stories high the building is. We typically require access points to the vertical stacks every five (5) to seven (7) stories depending on the configuration of the system.